Home » X-Ray Compliance Testing and Room Compliance (Explainer)
What do we know about x-ray compliance testing and room compliance in Australia?
In Australia and many other countries, regulations govern the use and installation of x-ray machines. These regulations ensure that safeguards are in place for the proper installation and safe use of x-ray systems.
One critical requirement is that x-ray rooms must have adequate shielding. This shielding protects both the occupants within the x-ray room and those outside of it.
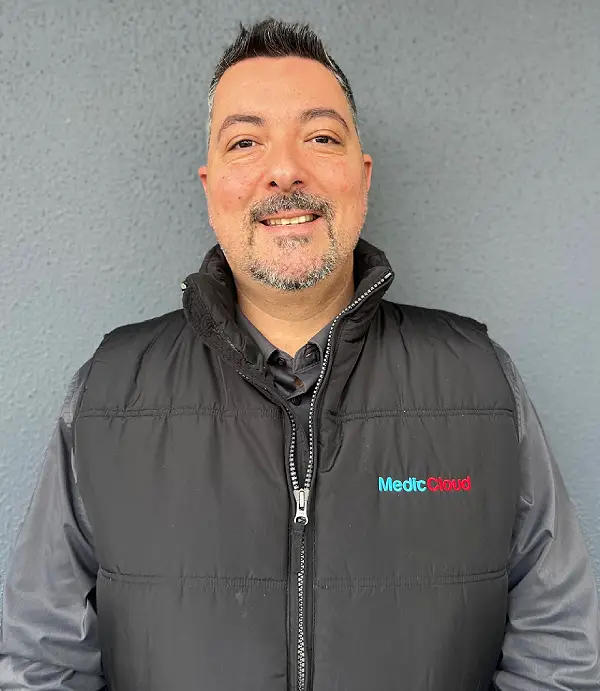
Sam, Medic Cloud Managing Director
What needs to happen before an x-ray machine is installed in Australia?
Before installing an x-ray machine in a clinical environment, the clinic must obtain the relevant licenses from local governing bodies such as the:
- Department of Health, Victoria
- Queensland Health,
- Environment Protection Authority (EPA), and
- EPA South Australia.
A key condition of the license is providing evidence of an approved shielding plan for the room. Once the shielding plan is approved, a builder can construct the x-ray room according to the specified requirements.
Licensed companies, such as RadTest Australia, typically provide shielding plans for the purchase, installation and operation of the x-ray machine RadTest Australia’s team of nuclear physicists is well-known for carrying out this work.
After building the room with the required shielding, the equipment can be delivered and installed. In certain states, compliance testing is necessary to:
- Ensure the room is correctly shielded,
- The operator has a safe place to stand while procuring x-rays, and
- Any doors, windows, and frames have adequate shielding to prevent radiation traveling out of the room.
X-ray machine room compliance example
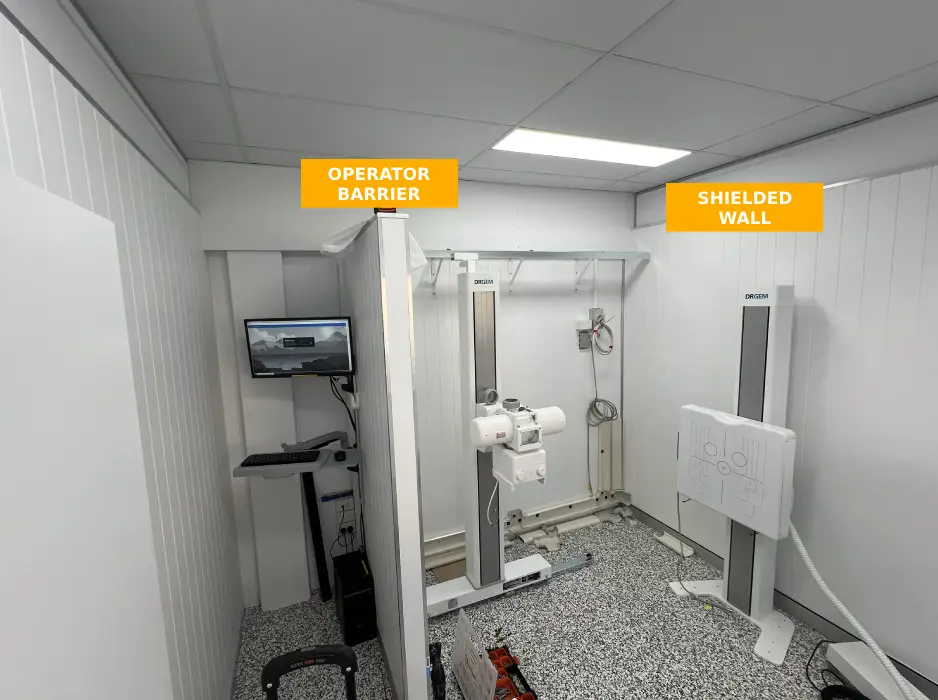
X-ray room compliance example
(R): Shielded wall prevents radiation leaving the room.
How do we test for x-ray compliance?
X-ray compliance involves testing the x-ray machine to ensure it adheres to various safety standards set by relevant governing bodies, typically under the Radiation Act of the state or territory where the equipment is installed. During the compliance process, several factors are evaluated, including but not limited to:
- Equipment stability to ensure no part of the installation appears or feels unsafe.
- Radiation leakage testing.
- The behaviour of the exposure switch (such as prep and expose).
- Functionality of Automatic Exposure Control (AEC).
- Linearity of the output from the x-ray machine with set mAs parameters.
- Accuracy of the output from the x-ray machine with predefined kV and/or mA/mAs.
- Brightness of the light emitted from the collimator.
- Accuracy of the collimator windowing and positioning on both horizontal and vertical planes.
- Distance of the exposure switch from the radiation source.
How often is compliance testing completed?
Victoria and Tasmania require compliance testing every two years. In all other states, the maximum interval between compliance tests is five years. Additionally, for Medicare, a preventative maintenance x-ray service must be performed every 12 months.
If you have any questions, reach out to us at Medic Cloud on 1300 658 103.
Read more blogs
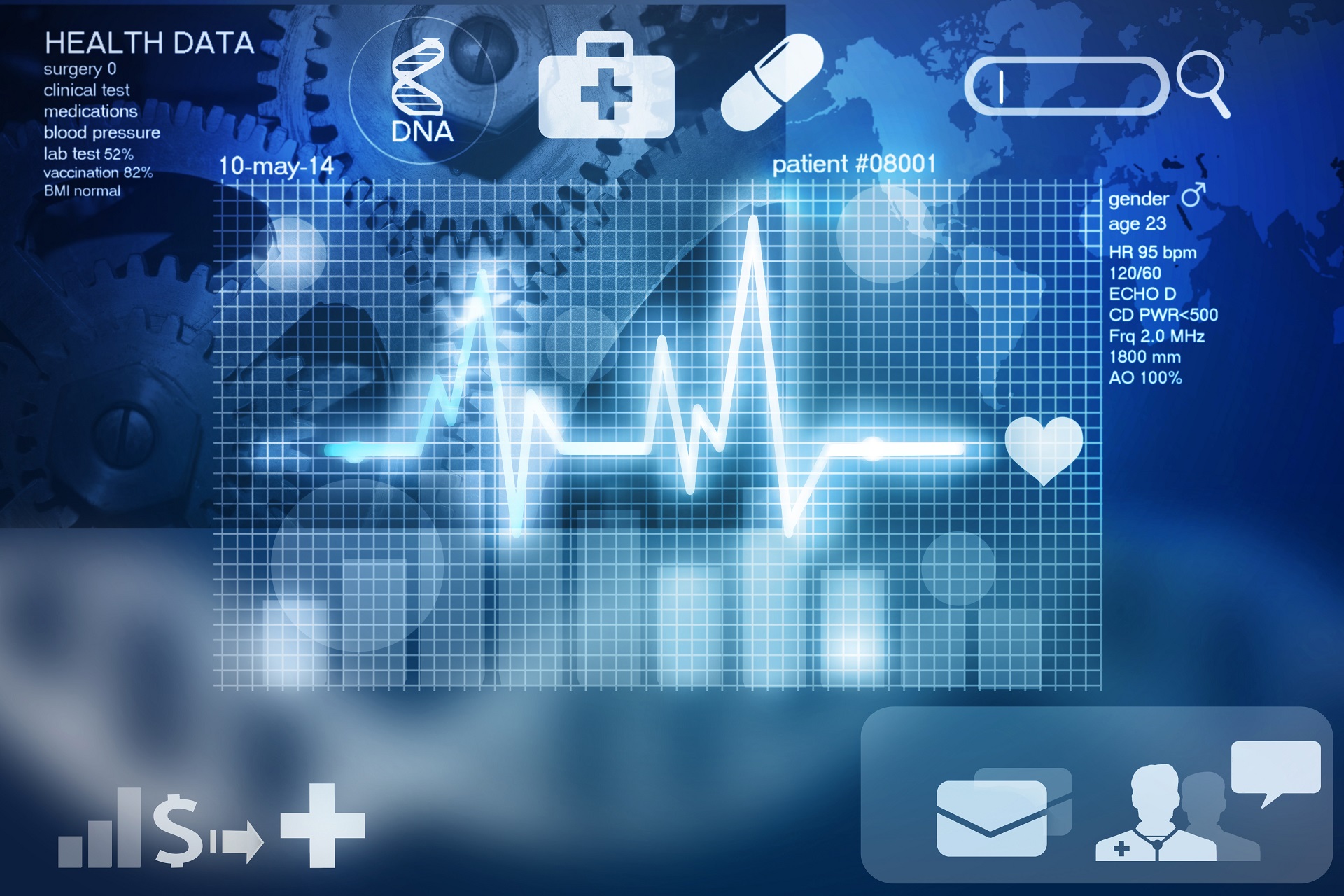
Subscribe to Medic Hub
Get the latest insights direct to your inbox.